Elevator Modernization
Elevator Modernization Is on the Rise Globally – Here's Why
- 十月 10, 2024
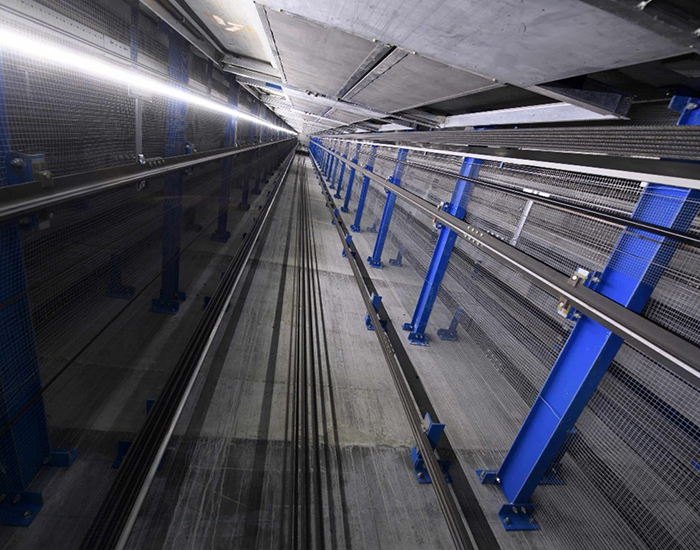
By Erika Goldstein, Otis Worldwide Corporation
In New York, Paris and Dubai, some of the world’s most iconic buildings are undergoing or recently completed upgrades to their elevators and escalators.
In New York, Otis wrapped up a 10-year project to overhaul elevators at the Empire State Building in 2021. It was one of the largest modernizations in the company’s more than 170-year history.
In Paris, Otis is in the process of updating the famed duolift™ elevators that carry millions of visitors each year to the top of the Eiffel tower.
And in Dubai, Otis will soon begin work to modernize elevators and escalators in the Burj Khalifa, the world’s tallest building.
These iconic buildings are part of a larger, global trend. Currently, more than 7 million of the world’s 21 million elevators are more than 20 years old – the age at which building managers begin to consider modernization. That number is expected to more than double to 15 million elevators in the next decade.
It presents a unique opportunity for building owners and facility managers to be a part of a massive overhaul of the world’s elevators and escalators that has already started, and is poised to run well into the next decade.
How we got here: population growth, urbanization and advanced technology
Population growth and rapid urbanization have increased urban density, and these trends are not stopping anytime soon. More than half of the global population lives in urban areas today, up from around one-third in 1950, That figure is on a trajectory to reach about two-thirds of the world population in 2050.
Rather than growing out into urban sprawl, many cities grew vertically. And now, many of the elevators and escalators installed in buildings in the last several decades are reaching the point at which they need an upgrade.
For elevators, this useful life is typically around 20 years. Past that period, aging equipment experiences more frequent and unexpected shutdowns. Spare parts may be less available, extending the duration of outages.
It can reach a point at which the costs and challenges of maintenance make an upgrade the more economical choice.
At the same time, advances in safety standards and technology – including artificial intelligence, predictive analytics, the Internet of Things, and touchscreen interfaces – are enhancing the performance of newer elevators and creating different expectations for passengers and facility managers.
And building owners and managers are turning to newer aesthetic components – elevator fixtures, cab materials, lighting and designs – to keep their buildings looking up to date and boost their appeal, whether in residential, commercial or other markets.
My colleague Tobias Stelzer, Otis modernization lead for Europe, Middle East & Africa, sees how these trends affect customer preferences every day.
Modernization is all about the customer,” says Stelzer. “They rely on our expertise and support in delivering the best service, product and project execution. This is where we, as a team, apply best practices and can continuously improve the customer experience.
Otis EMEA modernization lead Tobias Stelzer, at right, at a project site in Switzerland.
What is elevator modernization?
Simply put, modernization
is the industry term for an upgrade that significantly enhances the elevator or escalator. Modernization improves performance and reliability, boosts sustainability, and provides an opportunity to install the latest technology and safety features to elevate the passenger experience.
Elevator modernization projects vary from building to building. At its core, every modernization includes upgrading the system to the latest safety standards and regulations, and upgrading the controller, or "brain" of the elevator, to the latest technology.
Modernization projects also often include an upgrade of elevator cab aesthetics. Whether other components, like the motor, are replaced depends on the condition of the equipment and the needs of the building.
With our global experience and tens of thousands of completed elevator modernizations to date, Otis follows two guiding principles:
- Leave in place what equipment can stay, such as guiderails and other existing infrastructure, as long as they are in good working condition. This reduces overall cost and optimizes the environmental footprint compared to a complete replacement.
- Minimize disruption to occupants of the building, who are often present during modernization.
Environmental benefits of elevator modernization
Elevator modernization can offer compelling environmental benefits. For example, in the United States, we see a high concentration of hydraulic elevators, which operate using a hydraulic piston. They’re in low-rise buildings around the country and provide the biggest opportunity to upgrade to a more efficient elevator system that uses ropes or belts, significantly reducing energy costs.
Hydraulic elevators are mainly found in buildings like hotels, schools, and medical offices. This is a big area of focus for us,” says Otis Americas modernization lead Crawford Green. “In terms of markets with the biggest opportunities, people’s minds usually jump to big metropolitan cities. But it’s the cities like Grand Rapids, Michigan, and Fargo, North Dakota, or others of similar size and population density, where we have the most opportunity to modernize.
Otis Americas modernization lead Crawford Green, at left, with a mod project crew in Indianapolis.
A proactive approach to elevator modernization
Planned modernization work is easier to manage than unexpected disruptions from aging equipment. It can be incorporated into capital plans and long-term real estate investment strategy, benefiting building operations and passengers alike.
That’s why we believe elevator and escalator companies should take a proactive approach to modernization. This includes being transparent with facility managers about budget planning and potential costs, and making maintenance and repair data readily available. It’s about supporting facility managers to plan for a future modernization, rather than them being surprised by unexpected but necessary upgrades, or a long-term shutdown due to a hard to find, obsolete spare part for a dated elevator system.
Our customers value our expertise, and we work closely with them to make them aware of the life cycle of our products and consult with them as units age,
says Stelzer, the EMEA modernization lead.
As a growing number of the world’s existing elevators and escalators reach an age where modernization is necessary, we’re excited by the opportunity to share the latest in technology. It’s an investment that instantly upgrades the experience in any building, with benefits of improved safety, reliability and sustainability for building owners, facility managers and passengers alike.
Learn more about how Otis’ Modernization offerings are bringing new technologies to today’s buildings at https://www.otis.com/en/us/products-services/modernization-upgrades/modernization.
Erika Goldstein is Otis Vice President of Modernization. She was previously senior director of New Equipment Field Operations, and held roles in EMEA and Asia Pacific. In 2016, Goldstein co-founded Otis FORWARD, an employee resource group that provides mentorship and support for women in field operations and allies. She previously served in the U.S. Army as an Engineer Officer.